Fill level measurement
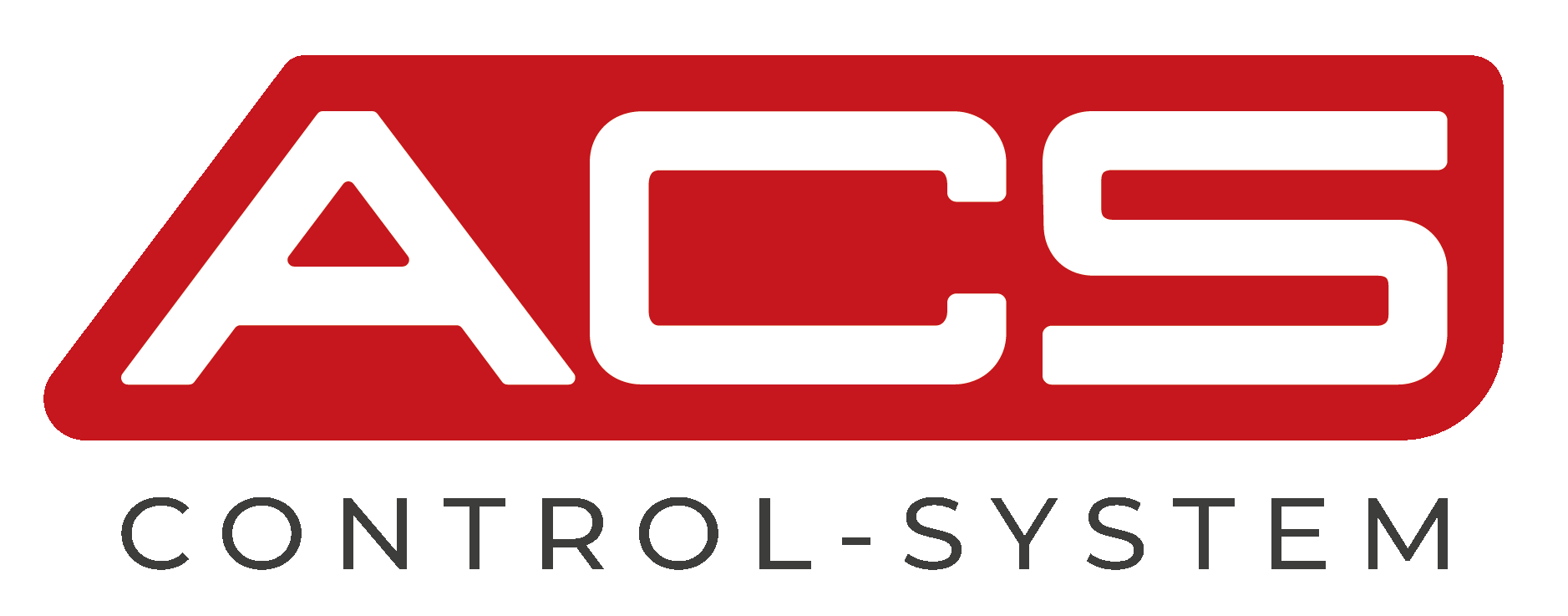
Fill level measurement technology from ACS-CONTROL-SYSTEM offers sensors for continuous measurement and point level detection in liquids and bulk solids. Due to the comprehensive selection of measuring principles and device types, we can offer a solution for every task. Fill levels or level measurement can be done with displacement sensors. For precise level control measurement, confocal sensors or laser triangulation sensors are typically used. For long ranges, such as silo fill level, laser rangefinders are used to measure material levels at a longer distance.
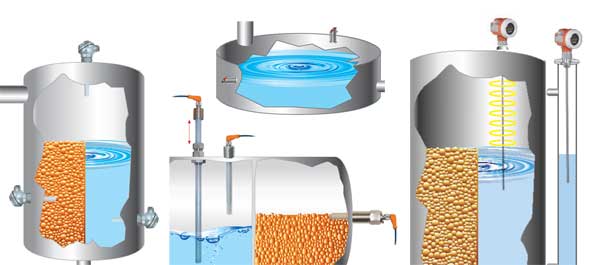
Hydrostatic level sensors measure the pressure of a liquid and convert it into a level value, since hydrostatic pressure depends on the level and density of the liquid, but is independent of the shape and volume of the tank. They are differential pressure sensors to which the pressure of the medium is applied and for comparison the second input is connected to the atmosphere or to an overpressure region in the case of a pressurized tank. Hydrostatic level gauges are used for homogeneous liquids in tanks without significant liquid movement and can be used for viscous liquids, suspensions and pastes.
Structurally, hydrostatic sensors are of two types: diaphragm sensors and immersion sensors. In the first case, the strain-gauge or capacitive sensor is directly connected to the diaphragm and the whole device is located in the lower part of the tank, with the location of the sensor diaphragm corresponding to the minimum level. In the case of a submersible sensor, the diaphragm is in the liquid and transmits pressure to the strain gauge sensor through a column of air sealed in the supply tube. Hydrostatic level transmitters provide high accuracy at low cost and simplicity of construction.
Ultrasonic level gauges probe the working area with ultrasonic waves, i.e. pressure waves with a frequency above 20 kHz. Structurally, such a level gauge consists of a transmitter and a receiver of oscillations made on a quartz plate, on which the voltage of the reflected signal is measured. The ultrasonic sensor is installed in the upper part of the tank. In this case the signal passes through the air and is reflected from the boundary with solid (liquid) medium. The level gauge in this case is called an acoustic level gauge.
The speed of ultrasound propagation depends on temperature, so temperature compensation is applied by means of a built-in temperature sensor. The operating range reaches up to 25 m with a measurement error of 1%. Ultrasonic level transmitters can be used for aggressive media and for media with a wide variety of physical properties, with the exception of highly steaming, highly foaming liquids and fine and porous granular bulk solids.
Radar level transmitters are the most technologically advanced level measuring instruments. Electromagnetic radiation from the microwave range is used to probe the working area and determine the distance to the object. Continuous level meters both emit a frequency modulated signal and simultaneously receive the reflected signal using the same antenna. The output is a mixed signal, which is analyzed using special software. Pulse microwave level transmitters emit a signal with pauses, in which the reception of the reflected signal occurs. The device calculates the transit time of the forward and reverse signals and determines the distance to the surface.
Radar level transmitters have no direct contact with the controlled medium and can be used for aggressive, viscous, heterogeneous liquid and bulk materials. They are distinguished from ultrasonic non-contact level gauges by their lower sensitivity to temperature and pressure, as well as resistance to dust, vaporization and foaming. Radar level gauges provide high accuracy, which allows their use in commercial metering systems, they allow to measure the level of media with low dielectric constant and, therefore, weak reflectivity. They are useful in vessels where various equipment is present, reducing the free area for radar operation.
The larger the size of the antenna, the stronger and narrower the signal it radiates and, at the same time, the better the reception of the reflected signal. The horn antenna is used in large vessels, allows to work with a wide range of media by dielectric permittivity, is applicable in difficult conditions and provides measuring range up to 35...40 m. The rod antenna is used in small vessels with chemically aggressive media or hygienic products, or when access to the vessel is limited by the small size of the nozzle. The measuring range is up to 20 m. The surface of the rod antenna is covered with a layer of protective insulation. The tube antenna is an elongated waveguide. It allows to form the strongest signal by reducing the scattering and is used in especially difficult cases in the presence of strong waves on the surface of the medium or a large layer of dense foam or in the case of media with low dielectric constant.
Conductive probes operate on electrically conductive liquids. When the probe is immersed in a liquid medium, the electrical resistance of the product is detected, a small alternating current flows between the electrodes, which is measured by the integrated electronics, and this measurement is converted into a switching command for the output relay. The switching signal is determined by the mounting position or length of the electrode. Due to their easy maintenance and reliable operation, conductive probes can be used for overfill and dry run protection as well as pump control in all industries.
Level limit switches of the vibrating type have a piezo element that excites the vibrating fork to vibrate at its resonant frequency. When immersed in a liquid or bulk material, the frequency of the fork's vibrations drops. This change in frequency is converted by the built-in electronics of the device into a switching command of the output signal. Pressure, temperature, foam and bubble formation and even viscosity do not affect the accuracy of the level alarm. Due to the ease of cleaning, the alarm is applicable in the food and pharmaceutical industries. It operates reliably in any mounting position and does not require adjustment with the product. The sensor is used in overfill and dry run protection systems on plastic granules, milk powder and tablets.